D2 Steel History:
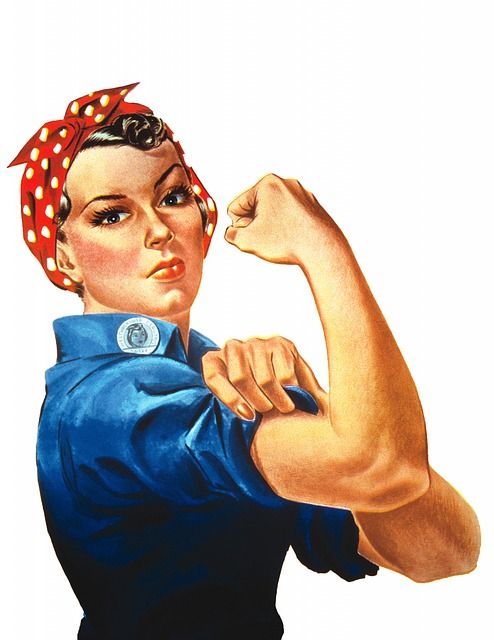
D2 steel’s popularity began during the “Rosey the Riveter” days of World War II. Back then, D2 steel was used to make dies for production lines. A die is pressed down to cut and create shapes out of softer steel.
To sum it all up, D2 steel was created to “punch” out large military vehicle/ airplane parts, that would then be hand assembled on an assembly line. D2 steel was not just designed to easily cut through other steels, it was designed to cut through other steels repeatedly, in a factory setting without major wear and tear. This work history enables us to determine the strengths of D2 knife steel. Most importantly, D2 steel is hard and resistant to heavy duty use.
D2 Steel Scientific Properties:
The D-series of the cold-work class of tool steels are considered high Carbon-Chromium Steels. D2 steel is air hardened and contains between 10% and 13% chromium (which is unusually high). D2 steel has a hardness in the range of 55 to 62 HRC, which makes is a very durable and high- end knife steel. D2 steel will retain its hardness up to a temperature of 425 °C (797 °F).
The chromium-rich alloy carbides in the D2 steel create excellent resistance to wear from sliding contact with other metal or abrasive materials. This steel has a high wear resistance and creates a tough knife that holds an edge. The very high chromium content provides better corrosion resistance than most tool steels and enables it to be semi-stainless.
Information Gathered From:
https://www.knifeart.com/d2steel.html
https://en.m.wikipedia.org/wiki/Tool_steel